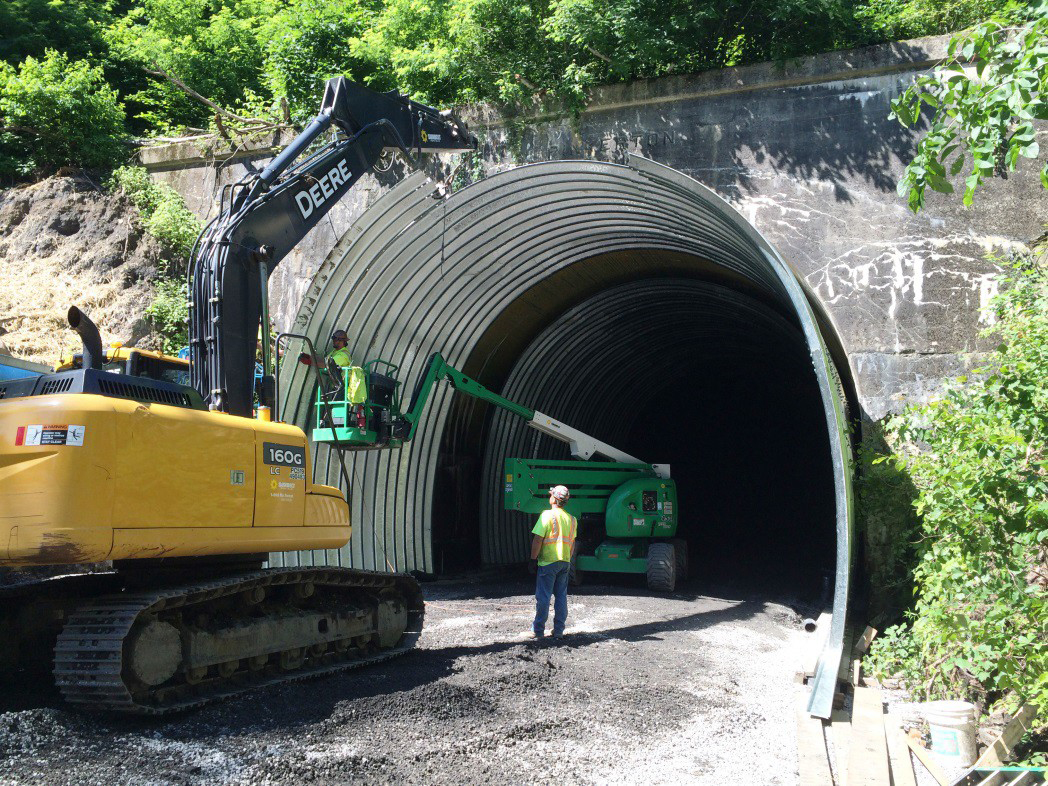
Pinkerton Tunnel Rehabilitation
Owner:Somerset County Rails-to-Trails Association
Engineer:Gannett Fleming Inc.
Contractor:Geobuild
Location:Southwestern Pennsylvania, USA
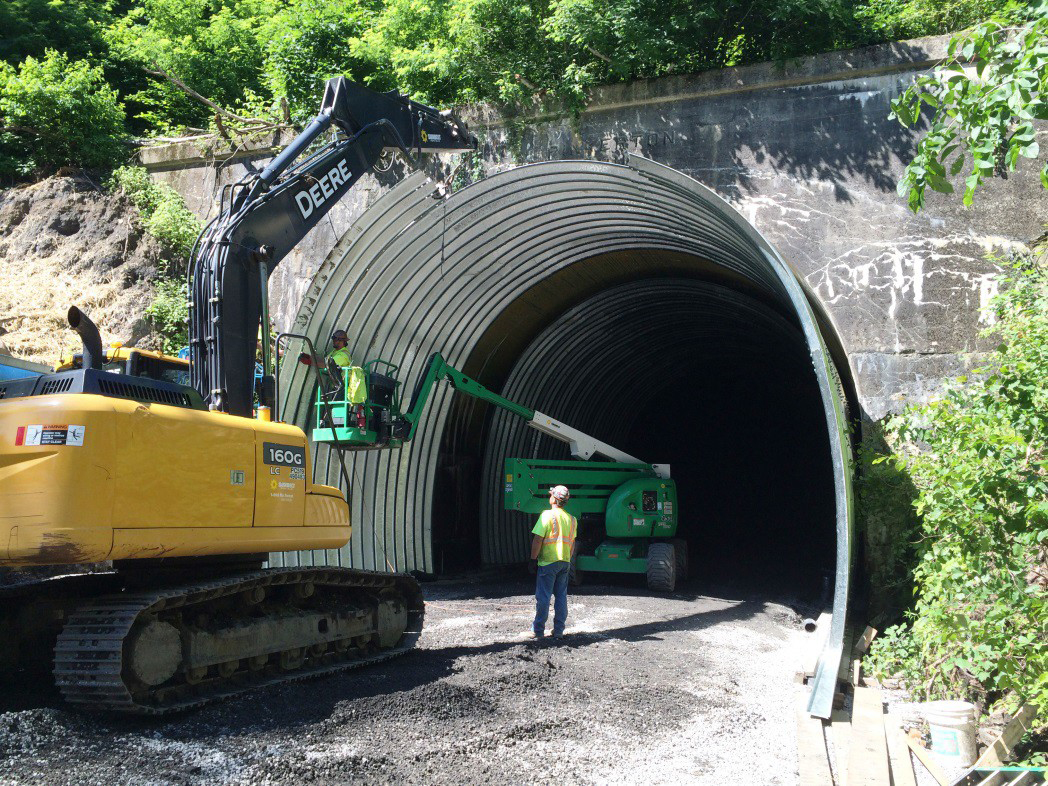
Product Utilized:
BRIDGE-PLATE®
The Challenge
The rail tunnel measured approximately 260m from entrance to exit. The customer requested a design with no struts or supports to hold the plates in place until the grout was set. A liner plate design of this size would require struts. An alternative deep corrugated structural plate (DCSP) design would not require struts, however unlike liner plate it would require bolting on both sides of the structure. Uneven deterioration within the tunnel caused its interior profile to vary significantly. The void space between the structural plate product and the existing tunnel also had to be minimized in order to reduce grouting costs.
The Solution
Armtec’s engineering department designed a Bridge Plate two-radius arch structure with an 8.3m span by 6.8m rise. In order to bolt the plates on both sides of the structure, 6m sections were pre-assembled and pulled into place along special slider plates set on the footings along the length of the tunnel. The 6m lengths of Bridge Plate liner were then bolted together using a custom designed internal joining mechanism. Over 1,000 plates were used – the equivalent of almost three football fields in length. In an effort to minimize the space between the concrete wall and the liner, Gannett Fleming laser measured the inside dimensions of the tunnel. Normal reline tolerances for structures of this size were 200 to 300mm. The consultant’s precise detailing was incorporated into Armtec’s manufacturing process resulting in a tolerance of less than 150mm. The precision production saved the customer an estimated $300,000 in grout costs.