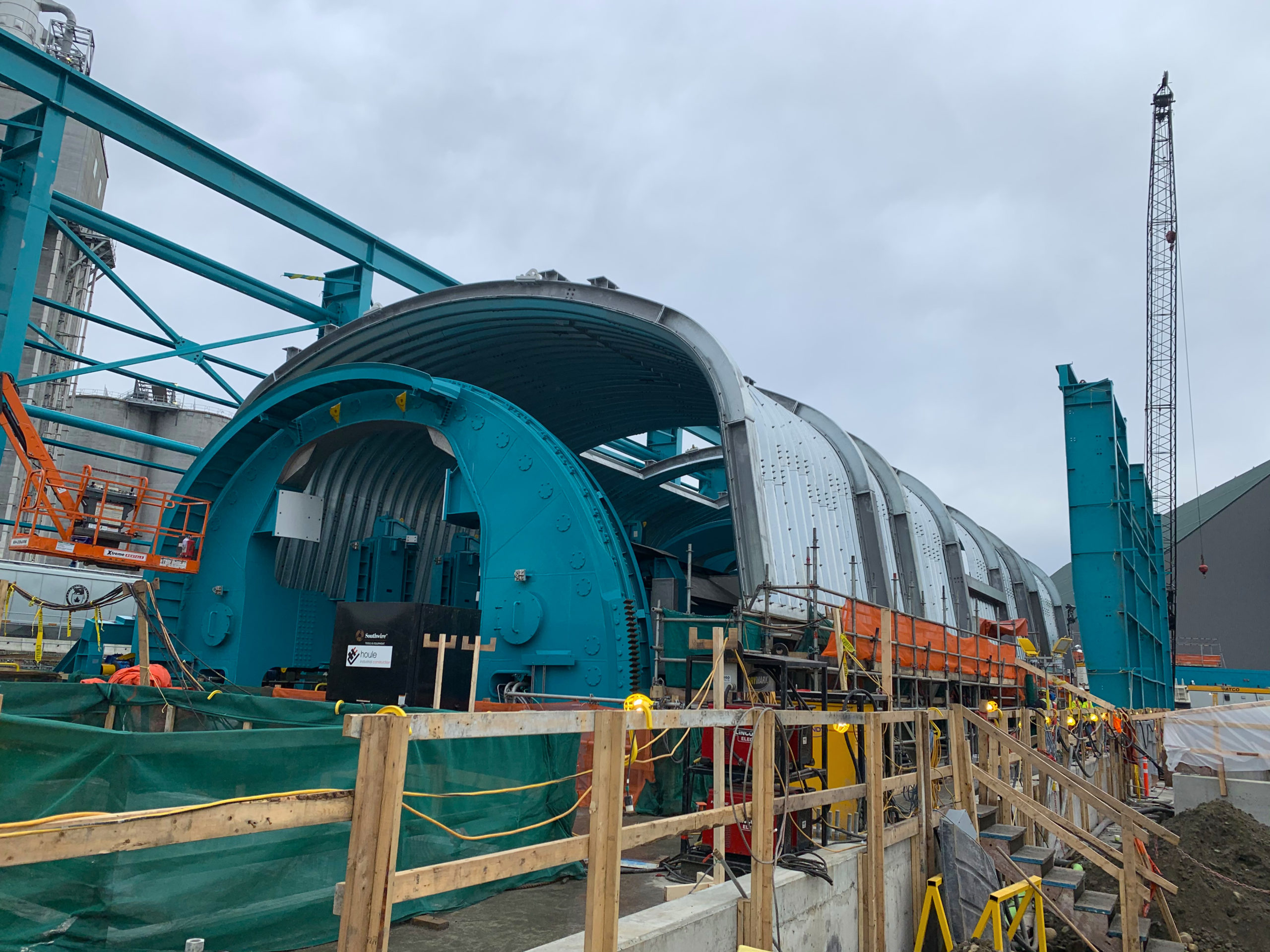
Neptune Bulk Terminals Dust Shroud
Owner:Neptune Bulk Terminals
Engineer:Neptune Bulk Terminals Consultant
Contractor:Graham Construction & Brymark Installations Group Inc.
Location:North Vancouver BC
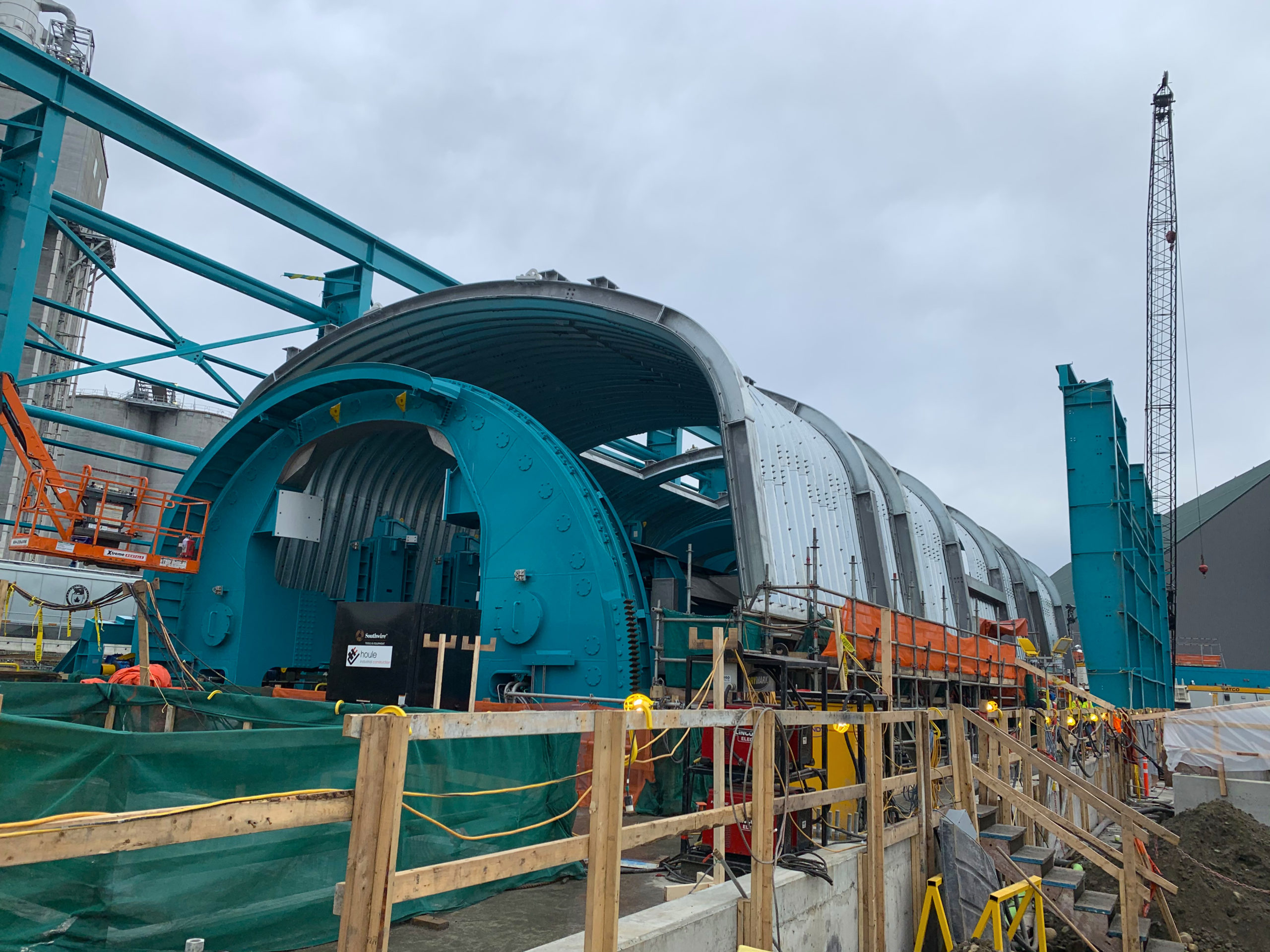
Product Utilized:
BRIDGE-PLATE®
The Challenge
Neptune Bulk Terminals required a structure to enclose two fully loaded coal railcars within the Dumper Building in order to prevent the spread of coal dust during rotation into the Tandem Dumper. Several parameters were critical in the design. The structure needed to be self-supporting while providing the necessary clearance. A three-section design was required to allow lifting of one of the sections for maintenance or derailment of the coal railcars. Each section required an access hatch at the top of the Shroud to allow the removal of drive motors for repair plus a side opening for a large ventilation blower. Finally, the additional load of walkways connected to the Shroud also needed to be incorporated into the design.
The Solution
Neptune Bulk Terminals reached out to Armtec through their consultants to inquire whether a segmental plate product could be constructed for the 11m span x 5m rise structure. Armtec proposed the use of Bridge Plate, a Deep Corrugated Structural Plate (DCSP) product allowing spans up to 18m. Additional curved reinforcing “Ring” beams would be required to frame the large openings in the dust shroud similar to mine hopper openings on corrugated plate reclaim tunnels. Armtec Engineers began design on the new Bridge Plate Dust Shroud to meet operational and installation requirements. The structure consisted of three sections allowing the necessary access while meeting external loading constraints. Engineers proposed 8.0mm thick galvanized steel to withstand the harsh industrial environment and deliver an extended service life. Care was taken to ensure the dust shroud would not interfere with other key operating equipment once installed. As the preliminary phase progressed, Armtec was able to accommodate a number of design changes throughout the project. With many moving components on the jobsite, Armtec produced over 75 pages of detailed shop drawings including the numbering of each plate and beam section to assist the Contractor during installation. Pre-assembly of the sections on a staging area, prior to hoisting into final position, allowed installation to proceed quickly and avoided fabrication over the open pit of the Dumper. The external Radius “Ring” Beams were attached to the sections and then each section was lifted by crane into their final positions over the Tandem Dumper. From the very beginning, Armtec was able to demonstrate its ability to provide a unique, one-of-a-kind structure by sharing past projects and engineering knowledge. The Bridge Plate Dust Shroud installation was successfully completed over a two-week period at the end of 2020, with remaining work scheduled for completion in Q1 of 2021.